Harpy – Sumo Bots 2009
This will be a collection of design information, videos, and photos of Harpy, the robotic sumo platform I built for the Science Olympiad tournaments in New York State.
Harpy’s drivetrain uses the motors that were used in La Cucaracha, only paired with larger, stickier wheels. It also has more capable, robust 4-cell 2.3Ah A123 lithium-iron-phosphate batteries capable of 70A continuous, but has a motor controller (Dimension Engineering Sabertooth 2×25A) that is akin to complete crap.
Harpy took a lot of cues from lessons learned building and competing with previous sumo bots. Its design goals were to be as simple and compact as possible, minimizing especially height and the length between the wheels and the front edge of the scoop. The first is to allow the bot to fit inside a foam-lined Plasticase 628 procase, which were offered at a discount to Techtonics, and to lower the center of gravity. The second was to maximize robot maneuverability—Harpy does not have swing around a large front “head” like many other robots do, but instead pivots about a point relatively fore to be bot. Its overall length was reduced, but if more length was require for space, it would have been added to the rear.
Harpy’s weight distribution (which is to place a maximal amount of weight upon tires and to minimize weight on ground contact points that do not contribute to pushing force) was heavily considered during design, but it was not a major design goal. Simplicity and robustness of the chassis were seen as more important and could not be compromised by design choices that improved weight distribution. Thus, a four-wheel design (driven by belts or gears from the two motors) was rejected, as well as a scoop with adjustable “ride height.”
Pursuing the goal of robustness and simplicity, Harpy features no flat horizontal load-bearing structures in its chassis. That is, contrary to most “standard” robot designs, there is no “base plate” or platform on which other components are mounted. Instead, Harpy has four one-quarter inch PETG plates standing vertically. They clamp onto the motors and clip onto the ends of the battery pack. In this way, the sturdy gearmotors and “shotgun barrel” style A123 pack (built from kit from the now-defunct Model Electronics Corp.) serve as the primary structural elements of the chassis.
These vertical plates are also connected to another vertical piece running left-to-right and to the scoop. That is more or less the entire chassis, and it is exceptionally sturdy and rigid compared to a traditional (and easy to build) platform-style design robot. In fact, even at the tournaments, Harpy uses no glue to hold its plastic parts together.
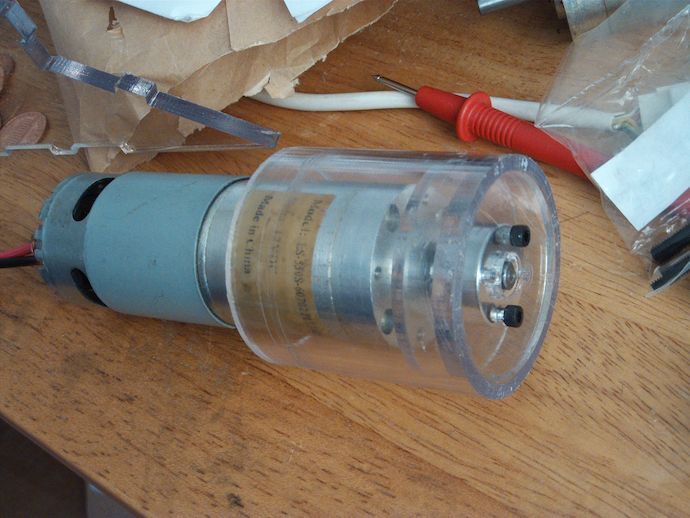
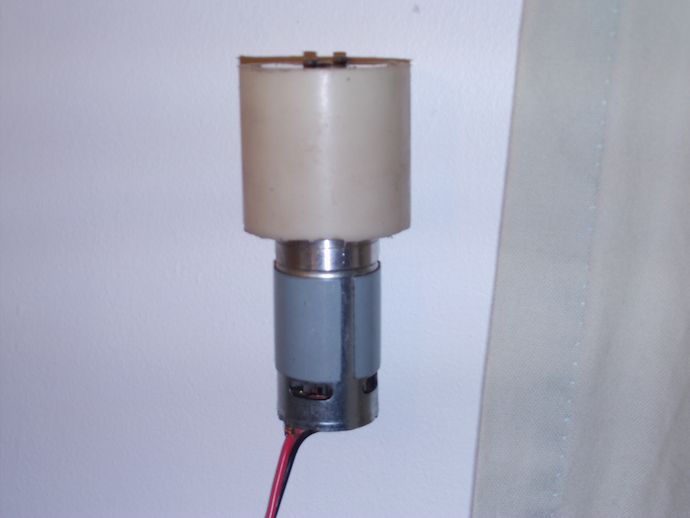
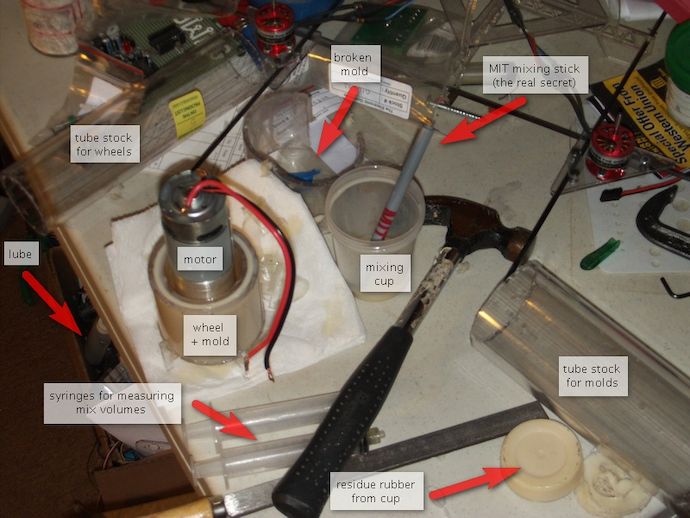
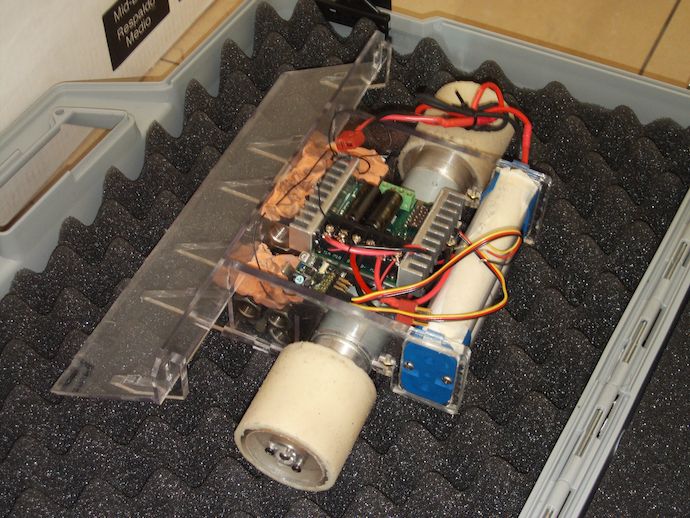
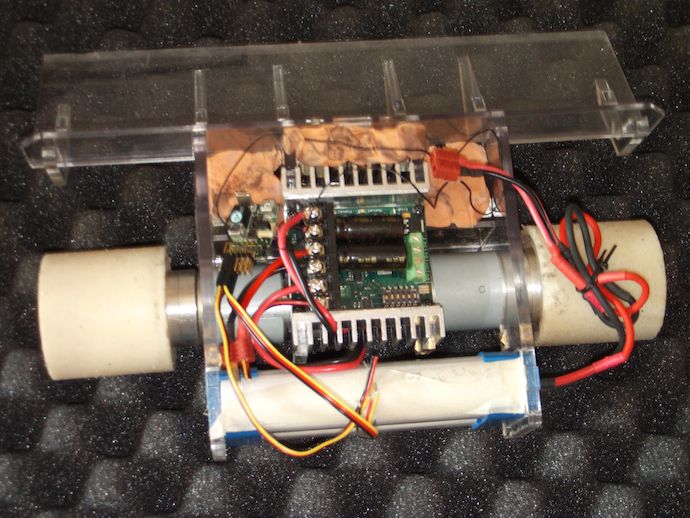
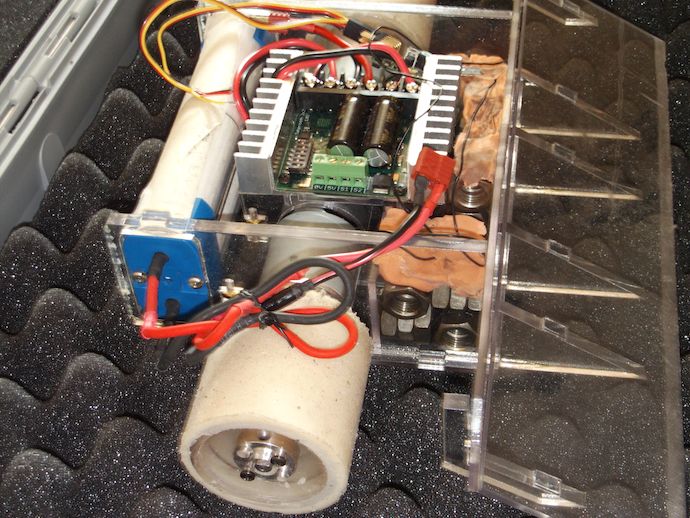
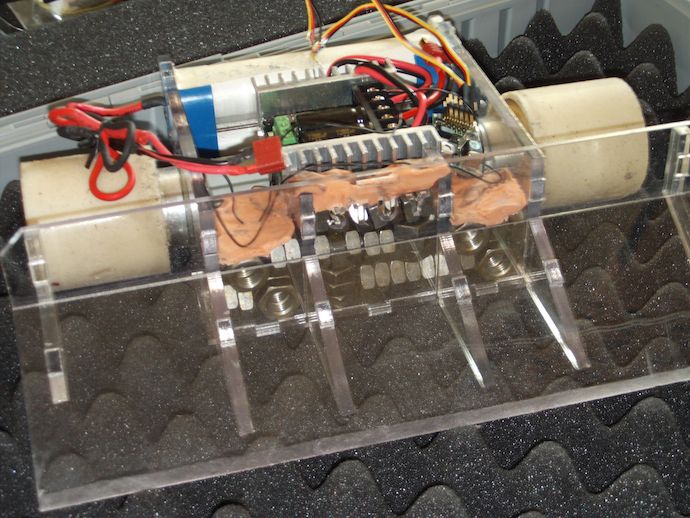
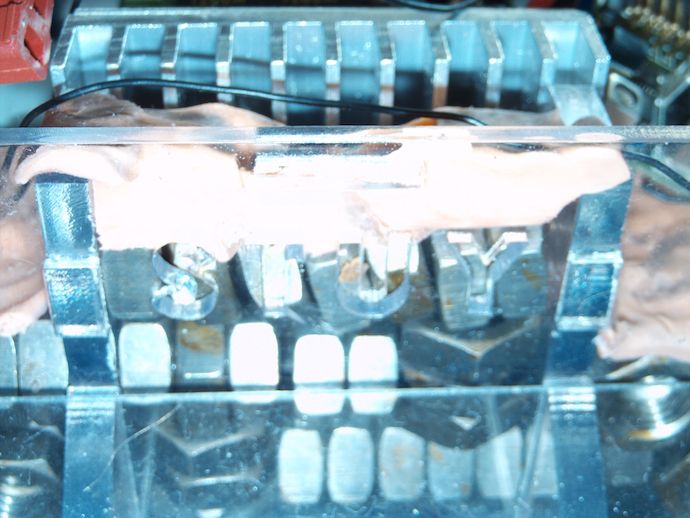
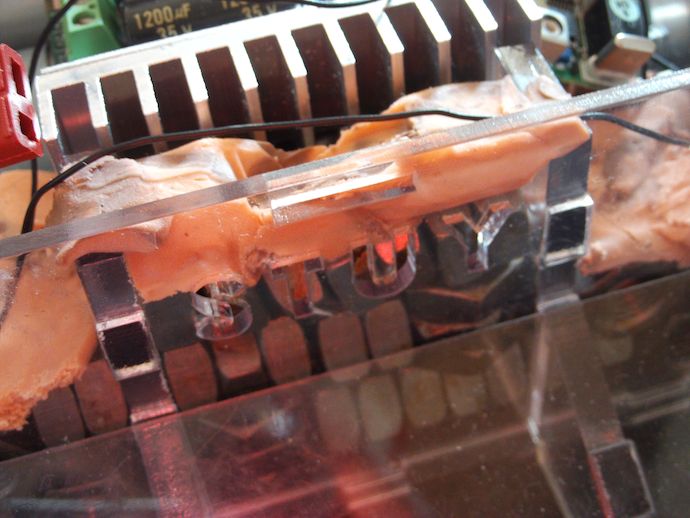
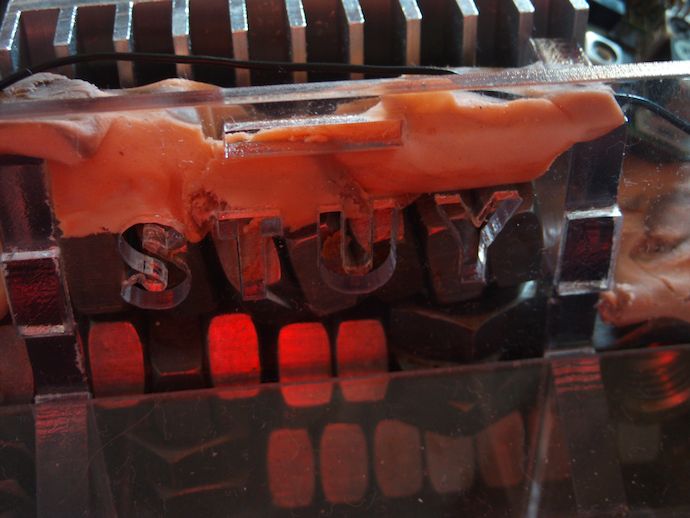
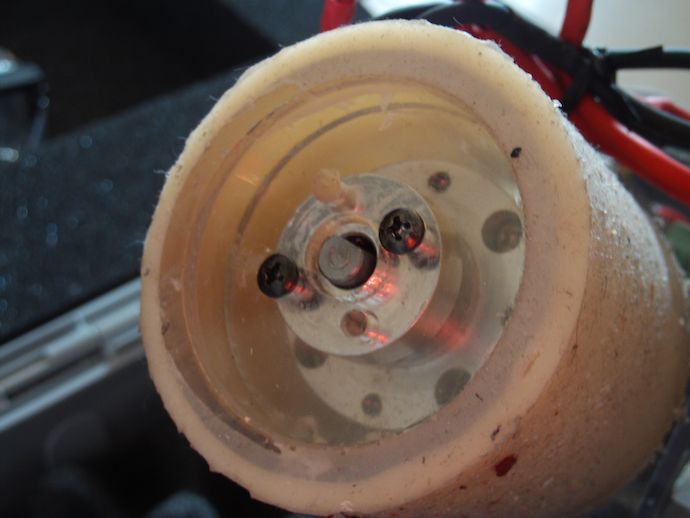
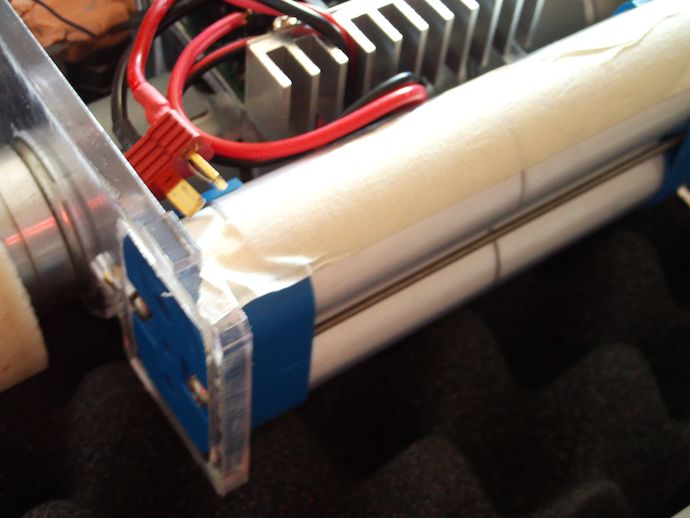
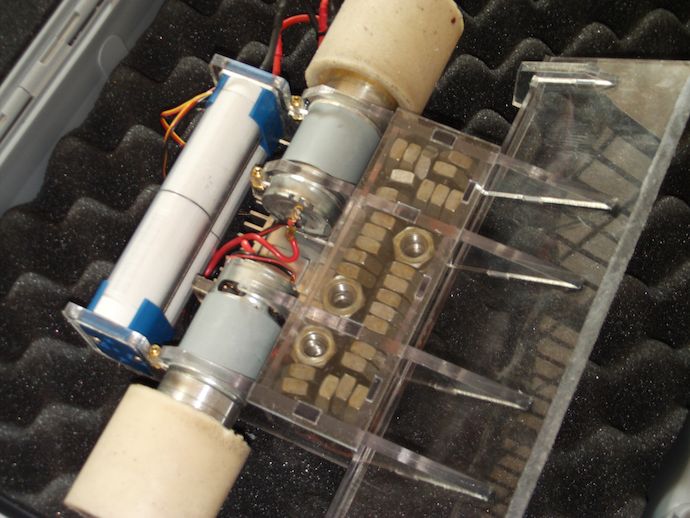
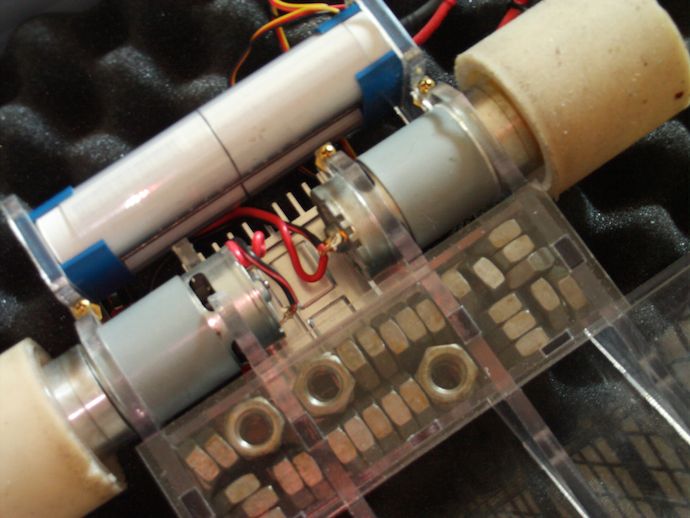
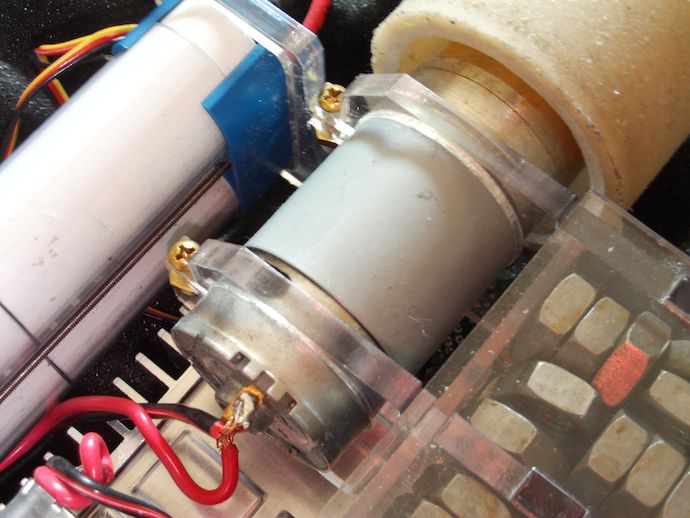
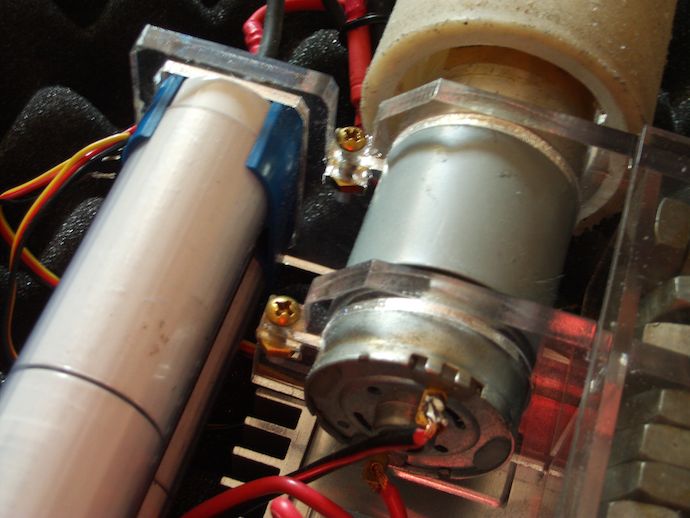
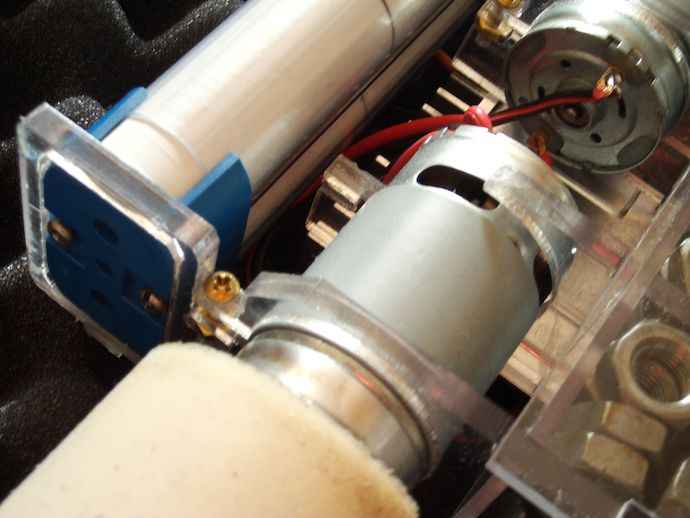
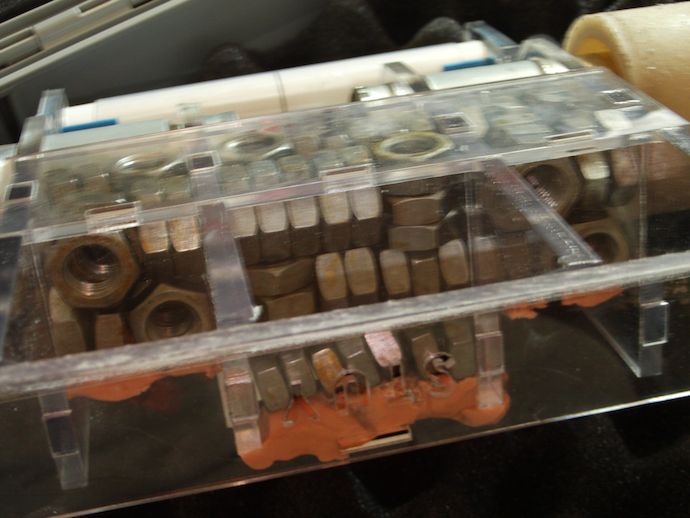
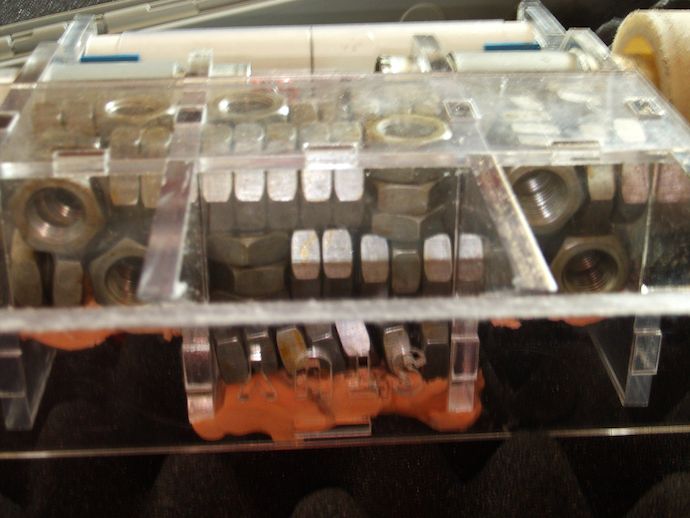
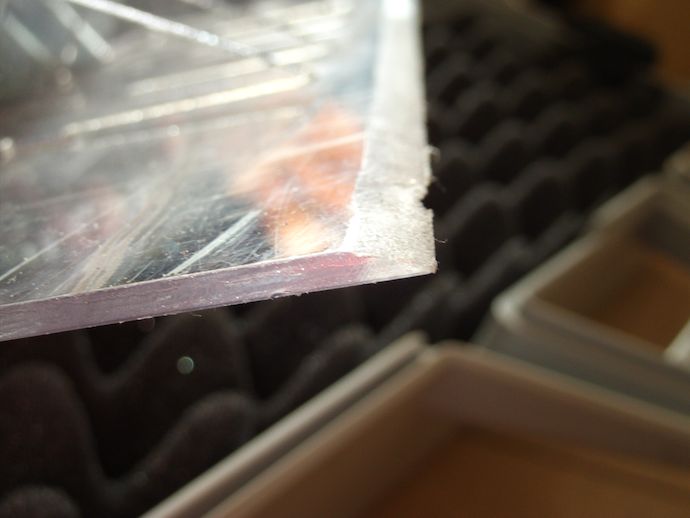
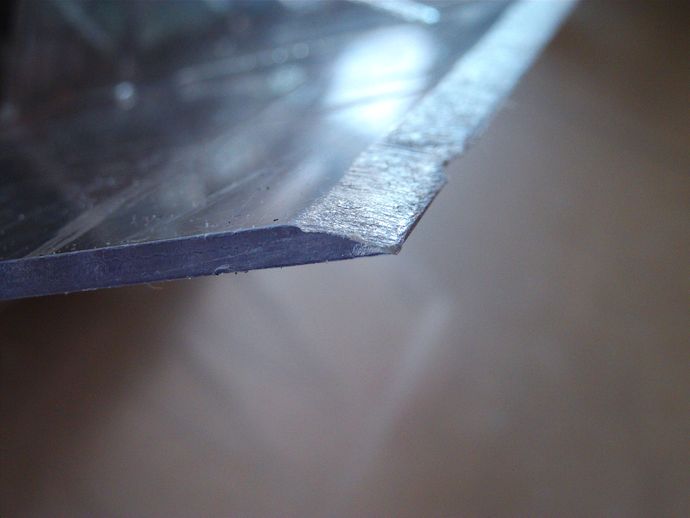
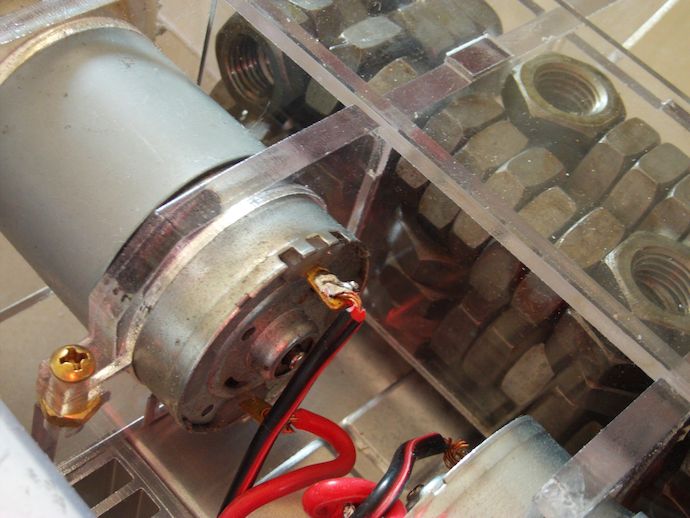
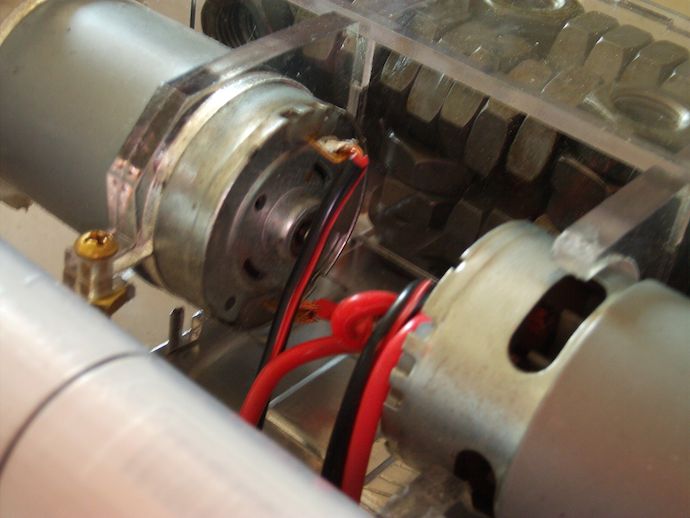
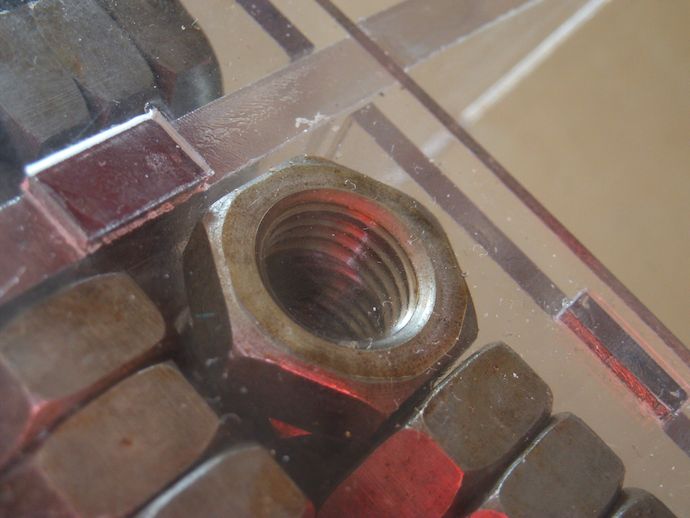
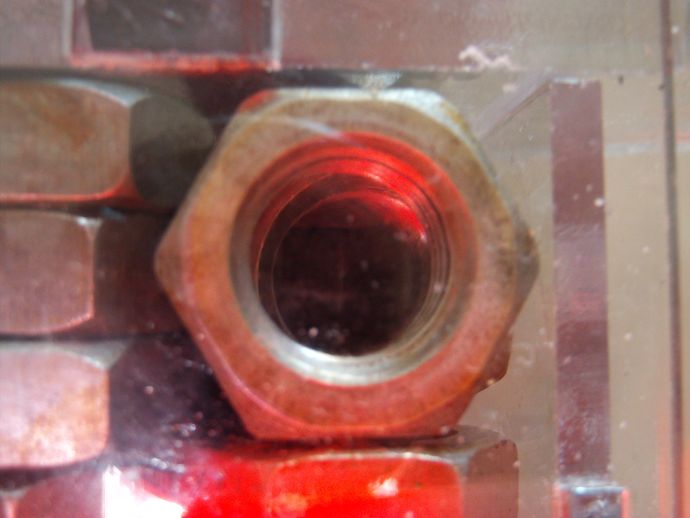
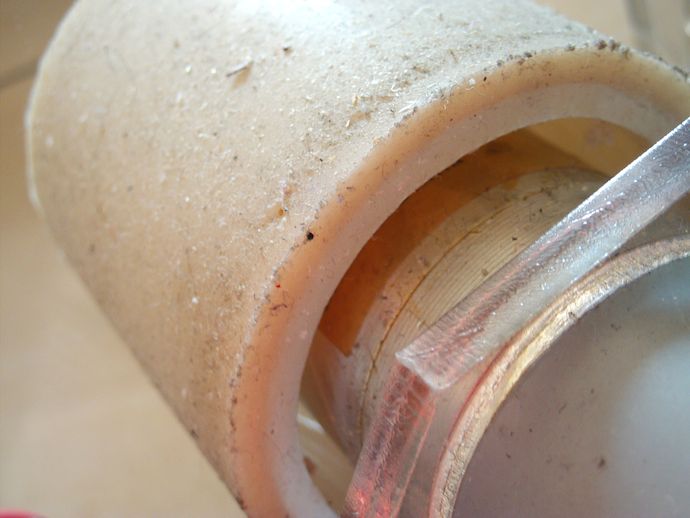
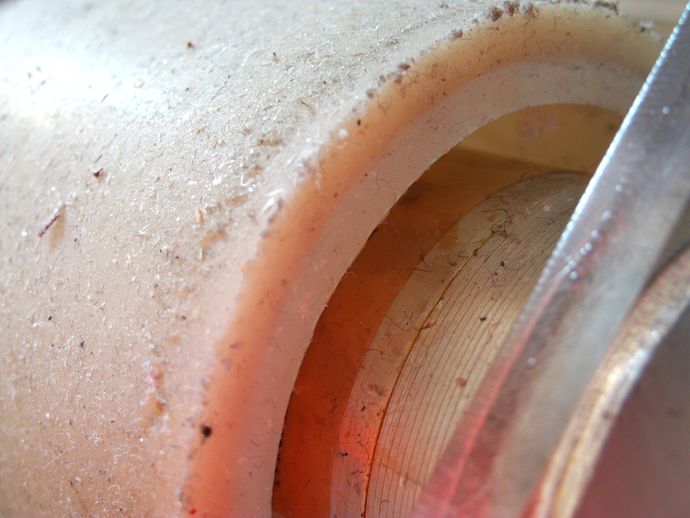
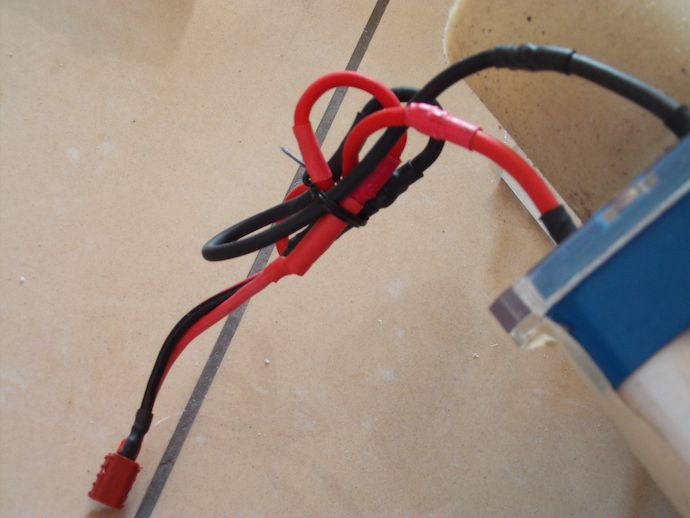
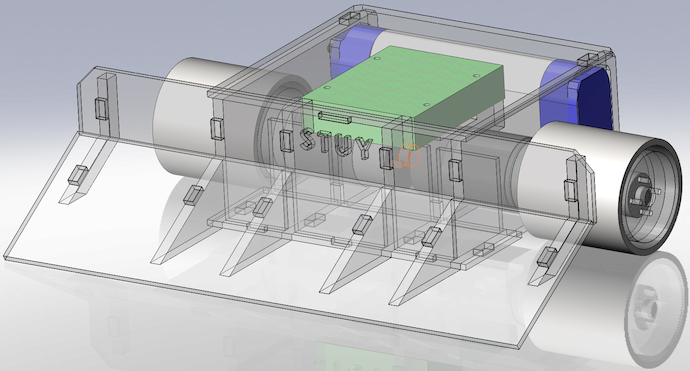
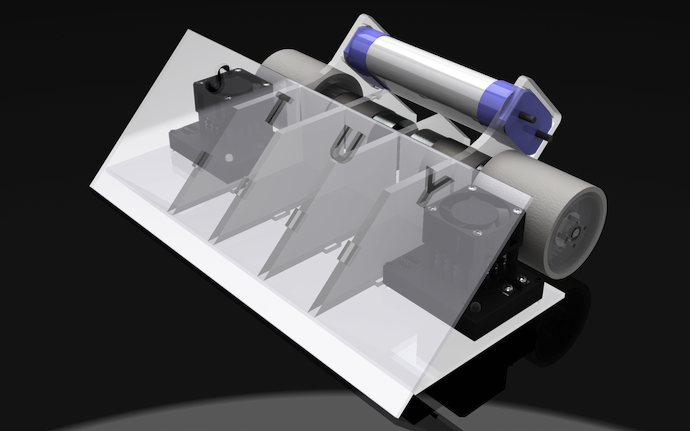
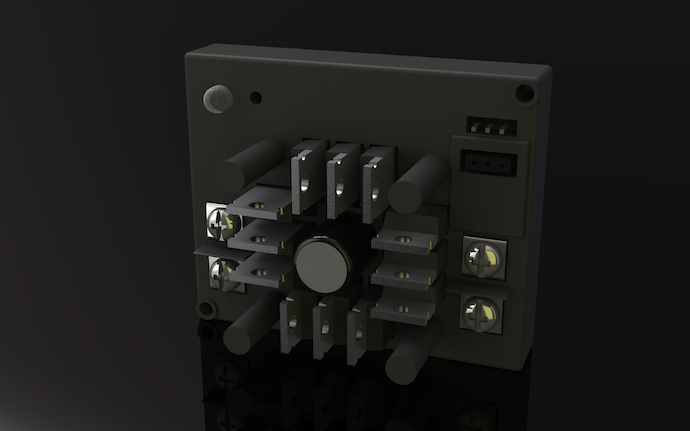
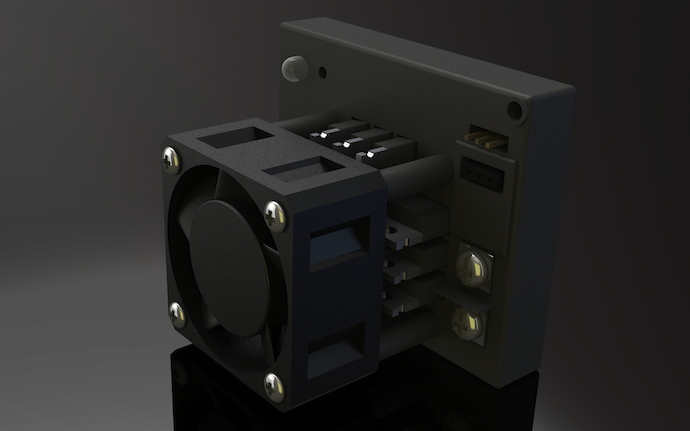
Harpy has immense pushing power, due to its 550-size gearmotors and custom-molded wheels. Thanks to cylindrical gearheads over the gearmotors that are flush and inline to the motor cans, Harpy has wheels that fit over the gearhead casing, rather than protruding out from the side of the gearmotors. The wheel forms are made from polycarbonate tubing (razor-sawed by hand) with inserts laser-cut from PETG. They are then placed inside a mold of similar construction. Pathway Polymers Por-A-Mold S-111 (which has a cured hardness of Shore A 20) was then mixed and poured into the mold.
The wheel and tire assembly was then broken out of the mold by cutting away the outer mold tubing on two sides, breaking the tube along one of the cuts, and folding the tube along the other cut. Think opening up a wrist shackle.
The resulting wheel and tire assembly were extremely sticky. After the wheel was mounted to the gearmotor, each of which is about a pound, it was found that the assembly could stick to vertical painted drywall indefinitely, and even upside-down to the ceiling. The robot, with clean wheels, can push more than 2 to 3 times its weight, depending on the condition of the wheels, alignment, etc. In fact, if the robot were to drive into a wall from a standstill, it can actually pop apart all of its plastic parts at the tab-and-slot joints, and essentially disintegrate. That is why it does not use any glue or plastic weld cement—if the structure can not relieve stress by popping apart at Lego-like joints, then it will crack and cleave.
New York City Regionals §
Match 1 – Stuyvesant Team C vs. Townsend Harris Team B
Match 2 – Stuyvesant Team C vs. Townsend Harris Team A
Match 3 – Stuyvesant Team C vs. Unknown Team
Match 4 – Stuyvesant Team C vs. Cardozo Team A
Match 5 – Stuyvesant Team C vs. Unknown Team
Match 6 – Stuyvesant Team C vs. Cardozo Team A
Match 6 – Stuyvesant Team C vs. Cardozo Team A (Redo)
Match 7 – Stuyvesant Team C vs. Cardozo Team A
All in all, Harpy’s mechanical design was extremely satisfactory, except that it has nowhere to mount the motor controller. Also, if the scoop is just a bit lifted up, then the rear rests on the batteries rather than the wheels, and it begins to lose traction, which can be seen in the video for Match 7. The motor controller is unacceptably unresponsive and underpowered, and a decision was made to replace them with Victor 883s, from La Cucaracha. These and other deficiencies resulted in Harpy II, which has not yet seen battle, but is a clear improvement upon Harpy I.
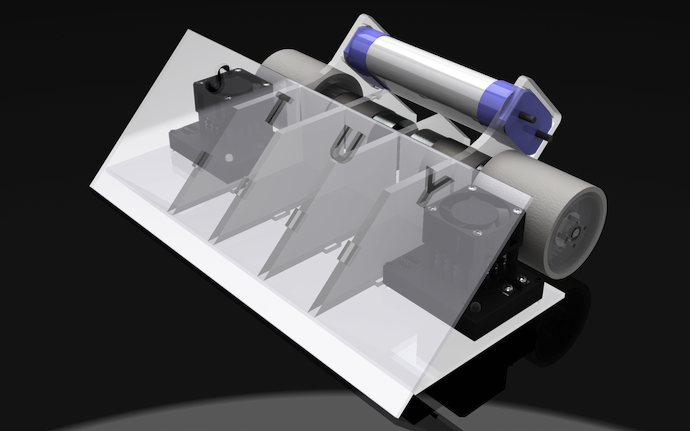