The Orange Involute
Big Data needed more drivetrain power. How do you get more of that sweet, sweet sensored brushless power?
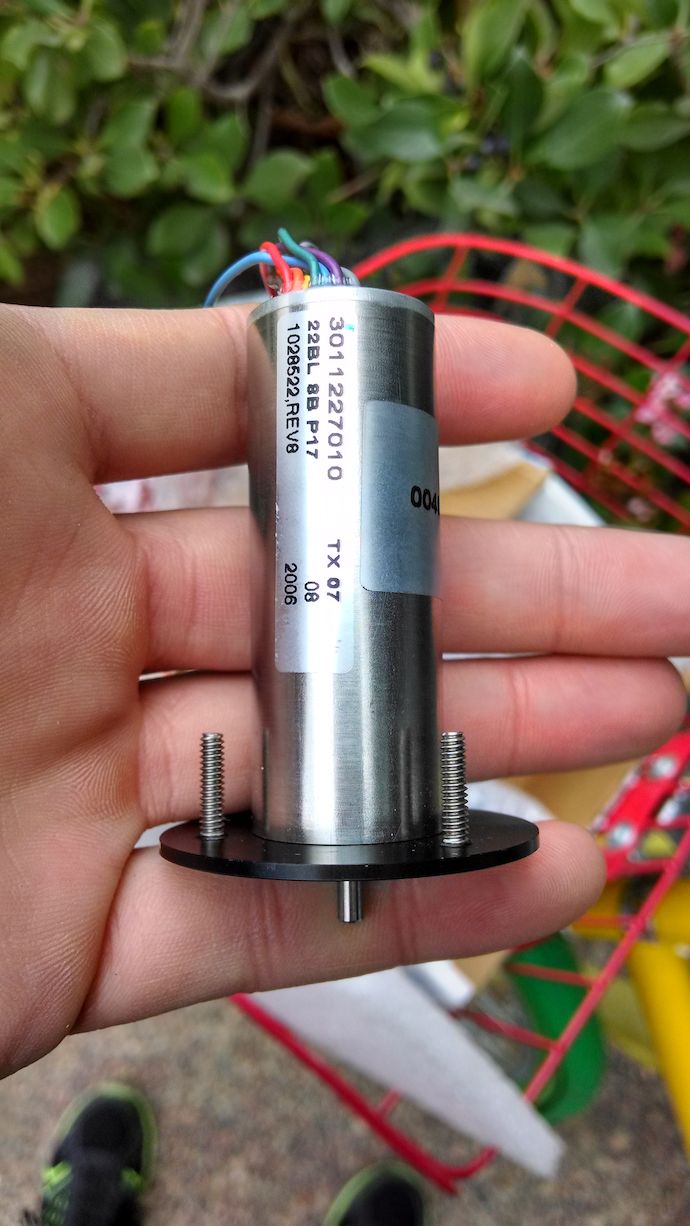
More motor.
These are eBay-supplied Portescap 22BL-8B-P motors, precursors to the current Portescap lineup of 22 mm motors. With different magnets on the rotor and a higher thermal resistance of 13 °C/W, they are rated for 20 W continuous rather than 70 W, but that’s still much more than a beetle weight (3 lb) robot needs, especially since drivetrain power comes in short bursts.
The mounting pattern in the diagram doesn’t quite match that in the photo. I’ll deal with that.
The more pressing concern is the outrageous speed. The hobby R/C world would describe this motor as a 1500 Kv “inrunner” with a no-load speed of 36800 RPM at 24V. With a continuous stall torque of 21.6 mNm and assuming 70 mm diameter wheels, each motor would have to be reduced at a ratio of 1:10.8 to be able to win a static pushing match against another beetle.
Even with that much reduction Big Data’s second coming would still have an estimated top speed of over 10 m/s (20 mph). The max power is limited by heat, not windings, so for short bursts the motors can drive Big Data to a full 1 G of horizontal acceleration at any speed within 90% of their top speed. Remember that this is the fastest that a robot can accelerate within the normal limits of traction (i.e., no tire adhesion, no magnets, no suction, etc.).
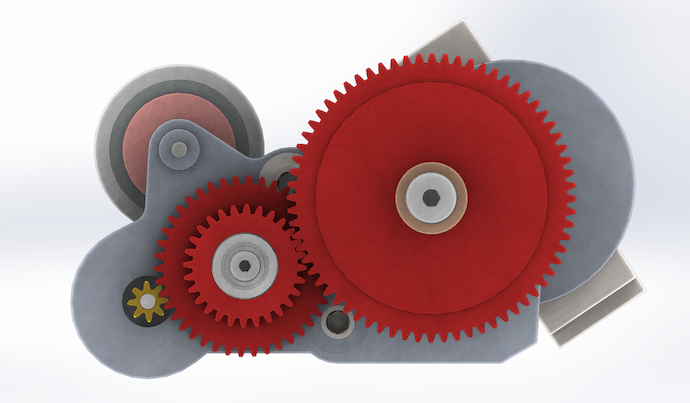
This design calls for at least two stages of gear reduction. I decided on 8:42 on the first stage and 28:68 on the second for an overall reduction of 1:12.75, using spur gears with a 0.8 mm diametral pitch (“Module 0.8”) and a 20° pressure angle.
I didn’t even know they made 8-tooth pinion gears, but there they are from Stock Drive Products*. Unfortunately, they don’t make a stepped spur gear with 42 and 28 teeth, so I had to make my own.
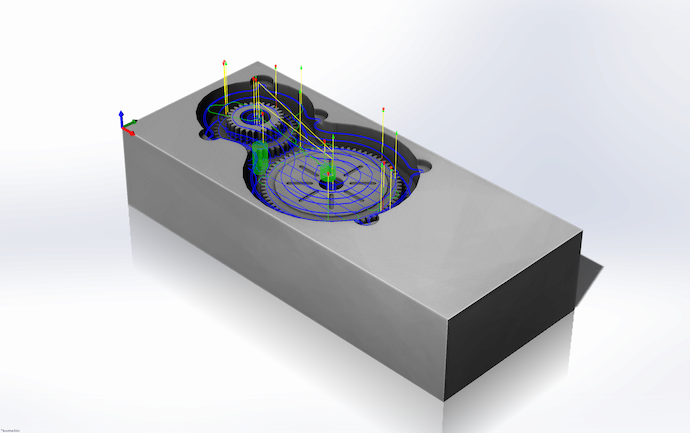
First I drew up the involute gear profiles as equation driven splines in SolidWorks and designed a machining solution using HSMXpress, my preferred computer-aided machining (CAM) package.
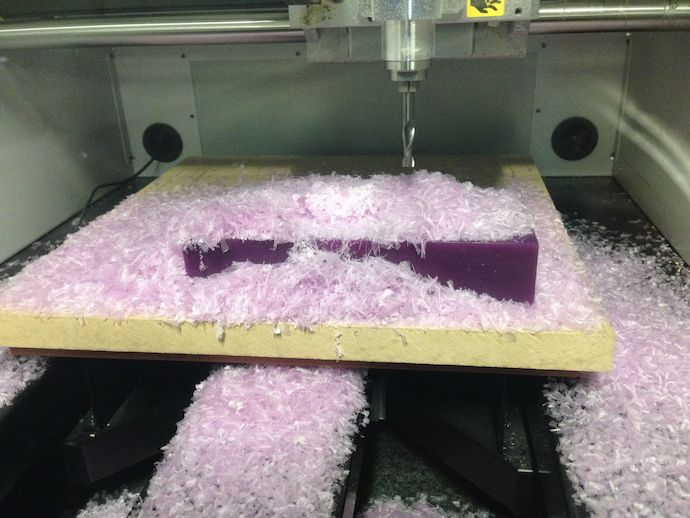
Then I milled the positive mold cavity from Freeman Supply’s “purple machinable wax,” which is basically hardened and plasticized paraffin. The machine is a Roland MDX-40† on loan to the Garage, the makerspace on Google’s Mountain View campus.
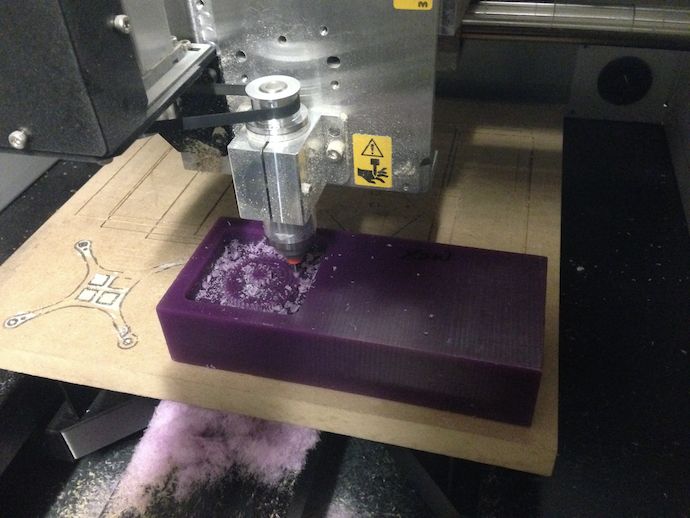
It gets pretty scary when I spin the 0.4 mm four-flute end mill to 15000 RPM and finish the teeth at over 250 mm/min. The high feed rate keeps the tool from melting the wax. Molten wax chips tend to stick back onto the mold and are tedious to get rid of.
No tools were broken in the making of these gears.
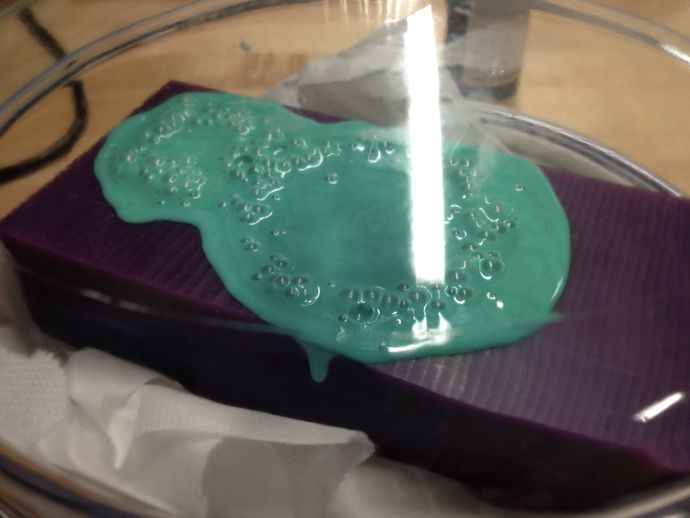
Next I mix up some Quantum Silicone QM 270 and drop it in the positive mold cavity. Under a strong vacuum, the air trapped under the silicone in the mold’s nooks and crannies balloon up and writhe to the surface, where they pop rather satisfyingly (and silently!).
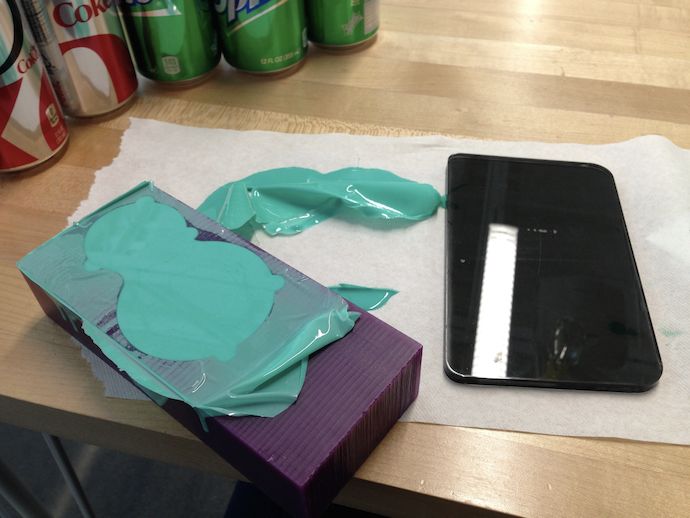
I kept the backside of the negative mold flat using a sheet of acrylic. Silicone doesn’t stick to anything, so this worked well.
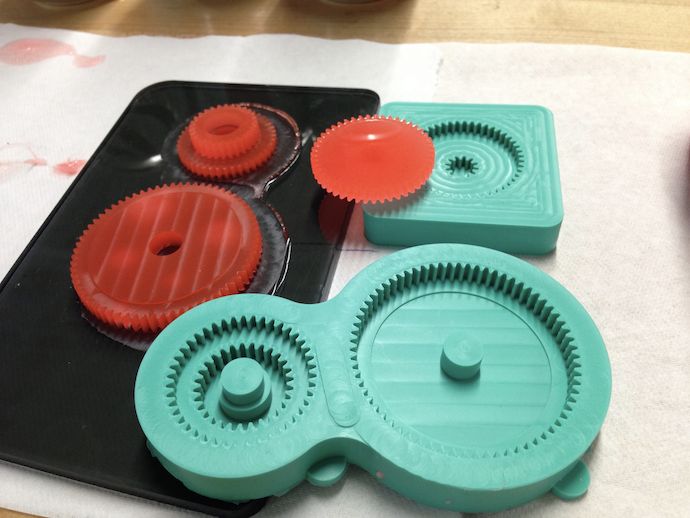
Now the negative mold is out and I have a reusable, flexible silicone negative for plastic gears. I dump in some Innovative Polymers IE-3075 and a lot of the orangest dye I have ever seen. Unfortunately, polyurethane does stick to acrylic.
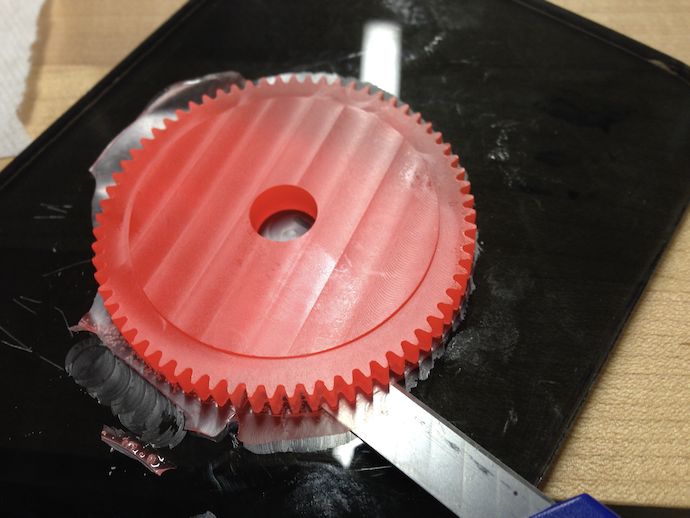
BAM, I got some gears. I love that the machining marks from the original positive wax mold are preserved through the process to the final part.
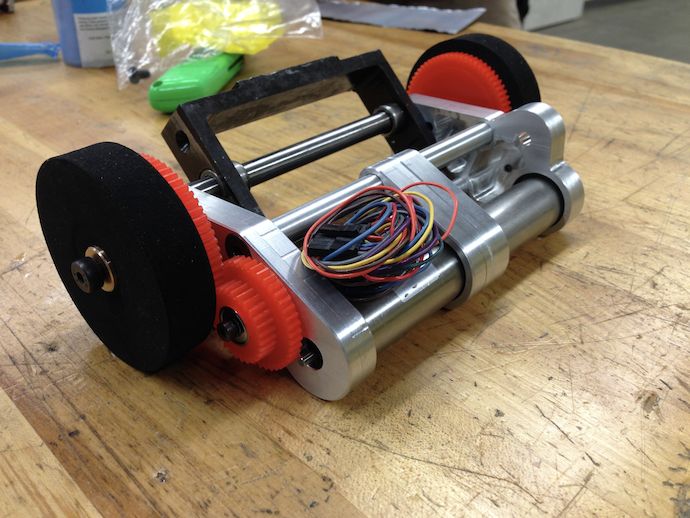
Seems to fit.
Thanks Dan for loaning us the Roland mill and thanks Michal for the superb CNC and resin casting guide.