Big Data: Test & Refresh
When I built the first Big Data in 2013, I was just getting to grips with my new surroundings. I even added the EVT moniker from my new job: in hardware development, “engineering validation test” means both testing the earliest prototypes and the prototypes themselves.
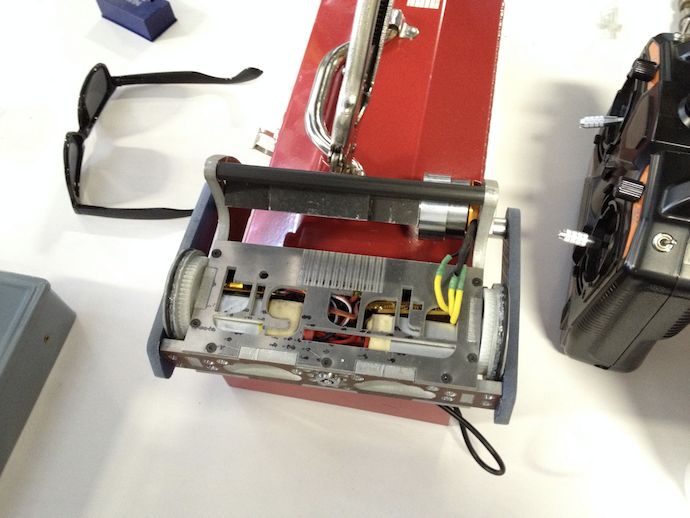
Spring §
I was overwhelmed by the Bay Area and toned down my typically masochistic design philosophy. I used a less-experimental (proven, even) weapon system* and relied on tried-and-true waterjet-style design.
I allowed one indulgence, which was building a new brushless controller appropriate for this scale and for the sensored 22 mm traction motors.
This is all great except the mechanical design didn’t work. The wheels were nowhere near the center of gravity, so that it didn’t really move except in short bursts, and the traction motors were each held in with five threads worth of four M2 screws on the face, which is to say they weren’t held in.
Summer §
Then came Big Data DVT (design validation test) and the start of the orange. Emboldened by familiarity with new capabilities, I used the CNC mills available to me and casted parts from polyurethane. Traction motors got even beefier while the weapon became more optimized… to the point of unreliability. The wheels shift so close to the center of gravity that just 0.54 g of acceleration causes DVT to pop a wheelie.
Naked wheels held on with un-threadlockered shoulder screws reflected an optimism and nonchalance to robot building of college days past. The trip to Atlanta, comped by association to Google’s recruiting at Georgia Tech and house calls to the local datacenter, laid excruciatingly bare how not to construct a vacation (or robot).
An aside: there’s a certain art to expressing yourself during a bot match. Jamo is a virtuoso both with the R/C transmitter and with situationally appropriate utterances of raw emotion. I might be on the other end of that spectrum with my twitchy fingers and a vocabulary of only “oh” and “no.”
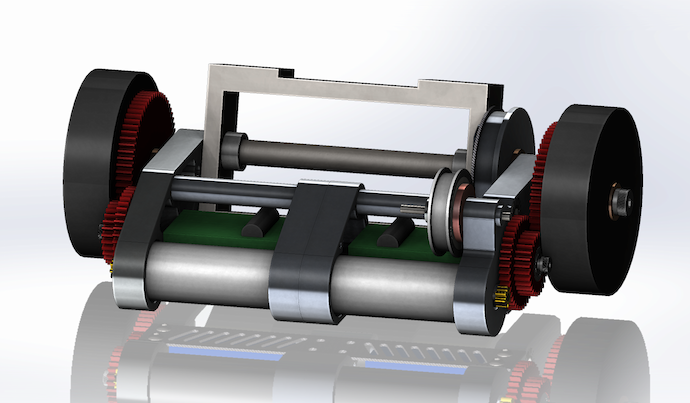
Also of note is that I’ve ditched machined horizontal chassis elements completely; i.e. there is no top or bottom plate that holds other components in place. I’ve favored this vertical construction style since building sumo in high school. I reused the round-standoff-between-plates technique used in Flapjack’s base because of the easy assembly and smooth curves it lends to a design. In Flapjack they were used to mount bearings for the shell; here, one of the beams—a hardened steel shaft, bored through and threaded on both ends—likewise supports the weapon from the milled aluminum “bookends.” To not load the screws in shear, the chassis is counterbored for the shaft to nestle into.
Autumn §
With all the cool logic of a frustrated toddler spurned at the toy store (“I WANT IT”), Big Data—and by Big Data I mean I—doubled down on the design out in the parking lot (“BUT BUT I NEEEED IT”). Production verification test (PVT) rang me up demanding none other than a weapon and drivetrain each taking up 30% of the weight. That left just 40% for a weapon motor, chassis (with all the bits & bobs), and electronics.
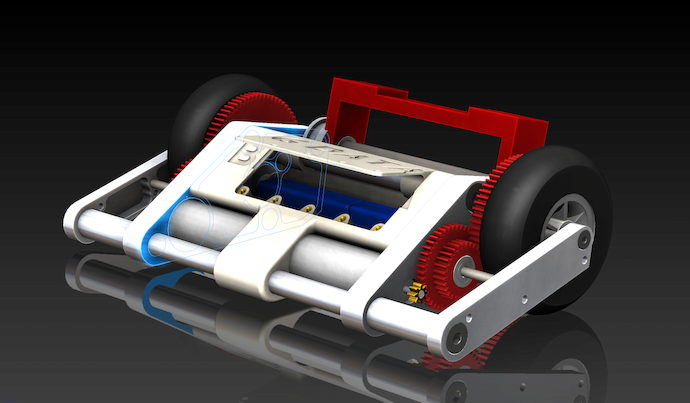
Whereas DVT used aluminum traction motor mounts fixed to the chassis’s two round beams, PVT’s drive motors were contained along with PCBs and batteries in a 3D printed “scaffold” wrapped around its three frame beams.
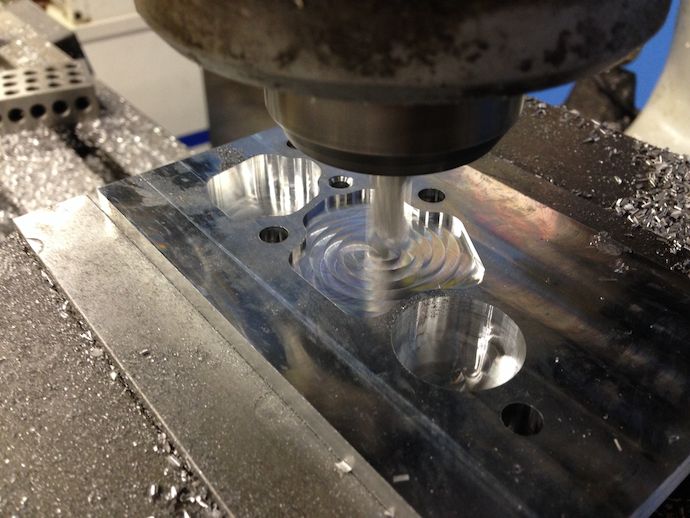
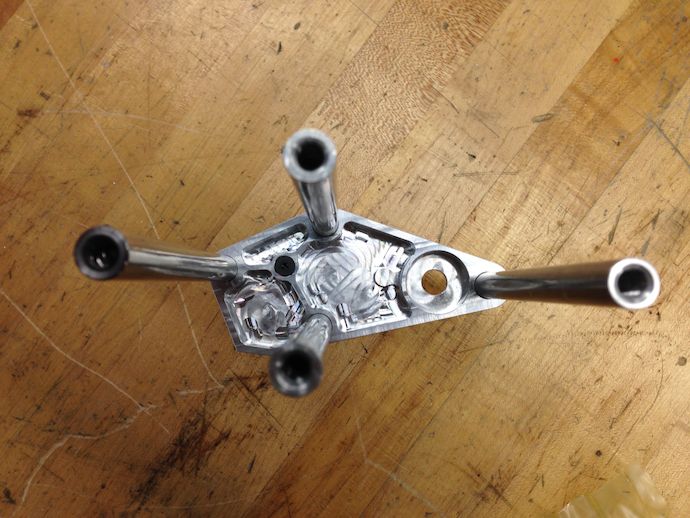
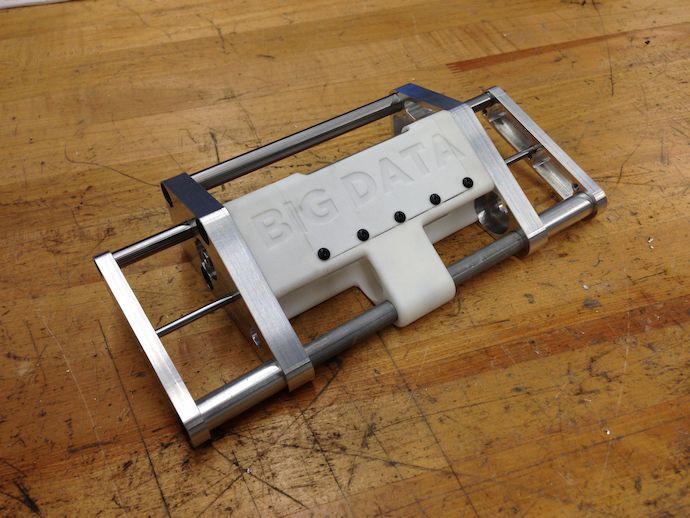
PVT was the first Big Data that entered combat with any semblance of armor. Its outside aluminum rails (15 g) served as double supports for the geartrain dead shafts and protected the wheels and gears a bit. They’re pretty.

Unfortunately, my custom motor drivers were less protected against the ESD hazards of dry winter air. Nor could the 3D printed scaffold withstand direct attacks from Chad’s saw and Kyle’s horizontal bar.
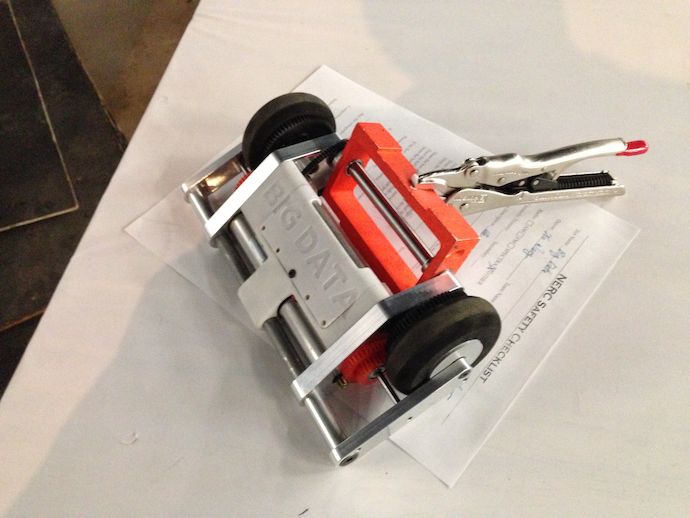
Why do I have to fight Georgia Tech RoboJackets?
WHY DO I HAVE TO FIGHT MY ROOMMATE?
KYLE NO MY RECEIVER AND BATTERY
PVT was underweight by at least 80 grams, and the frame shows basically no damage. Its access hatch made it much easier to work on than any other Big Data. If it weren’t for the too-wimpy weapon motor and that I misplaced half the chassis, I’d even consider using it again.
Winter §
I sold out. Brushless traction power affords me ridiculous speed but I’m not a good enough driver nor do I have enough time to practice to take advantage of that. And to be honest, I was getting a tad bored with this design.
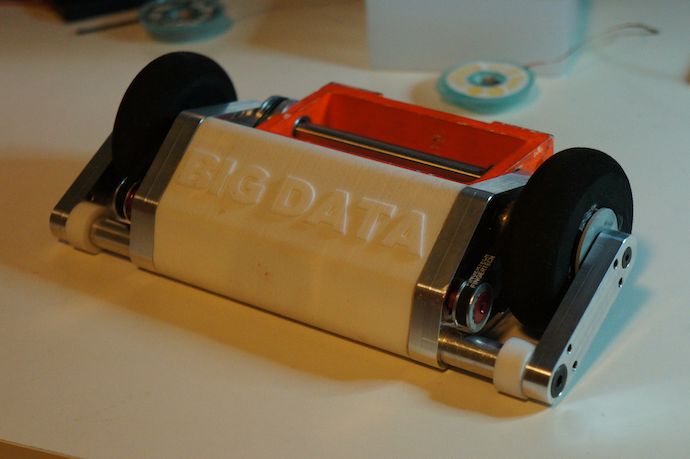
I acquiesced to the voices calling for a bigger weapon motor and smaller brushed traction motors. Big Data 4 finally has armor, and loads of it. I even tossed in my first ever wedges in combat.
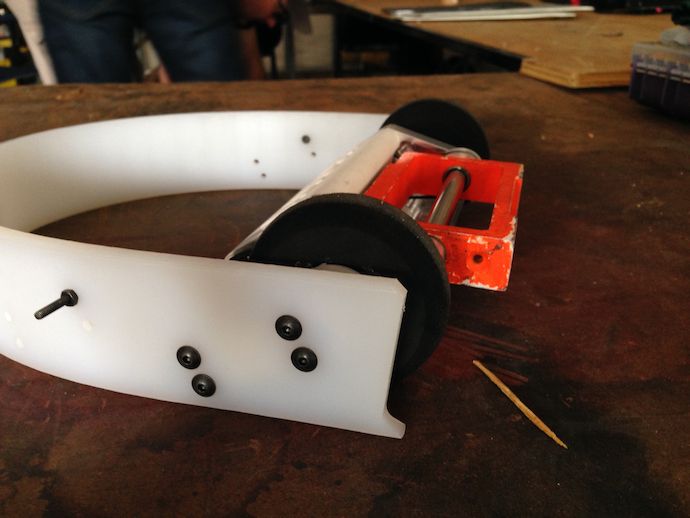
Although at DragonCon 2015 I kind of just knifed those in.
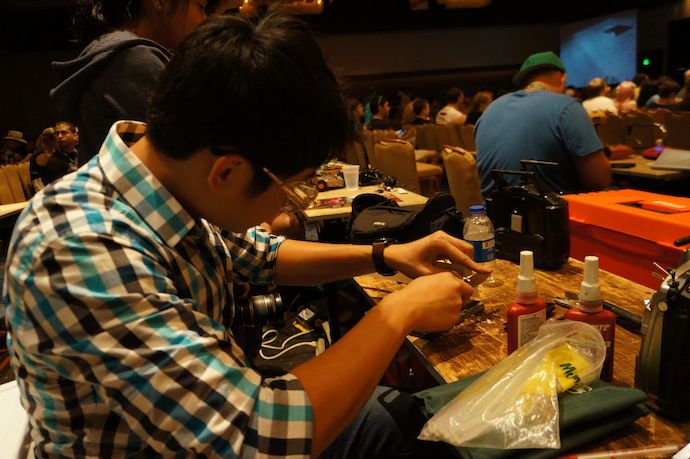
Fear of Design Spaces §
Another aside: I suffer from what I call creative agoraphobia. I’m paralyzed by too open of a design space, too many free variables, too few constraints. When I’m designing, this is the screen that panics me the most.
Having a free-to-use weapon bar and a gung-ho attitude to brushless traction were “hard” constraints that helped shape the last three Big Datas. I’ve heard that called “component-based design.”
Conversely if I consider the frame design a fixed establishment, transformed from free variable to set constraint, it gets easier to tweak other components I took for granted, like the silly-ly large traction motors. To get a design that worked, it was time to back off from those Portescap motors.
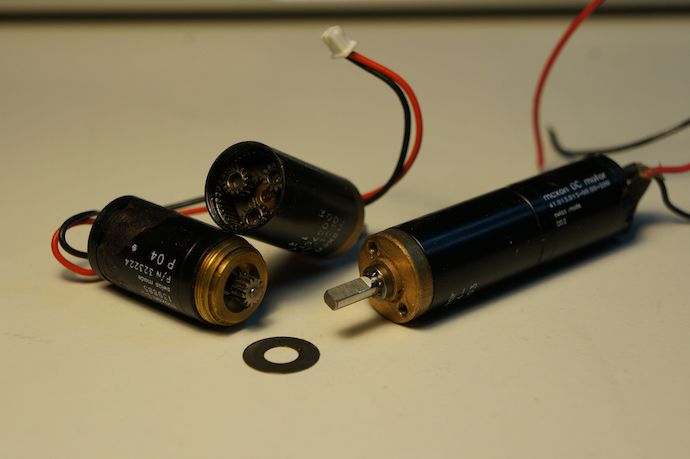
These are 13 mm diameter Maxon 67:1 gearmotors, sold as “235 RPM” units on eBay. They’re… OK. The construction is great, with large robust steel gears and gearhead mating threads built into the motor itself. But, they’re definitely slow for beetleweight combat and their precious metal brushes do not enjoy overvoltage operation at all. Maybe they become more useful after removing a stage of planetary gear reduction.
For now, they serve to provide slow but torquey drive traction for Big Data 4.
In its debut fight, BD4 promptly gets bottomed out like a Google shuttle at 23rd St.
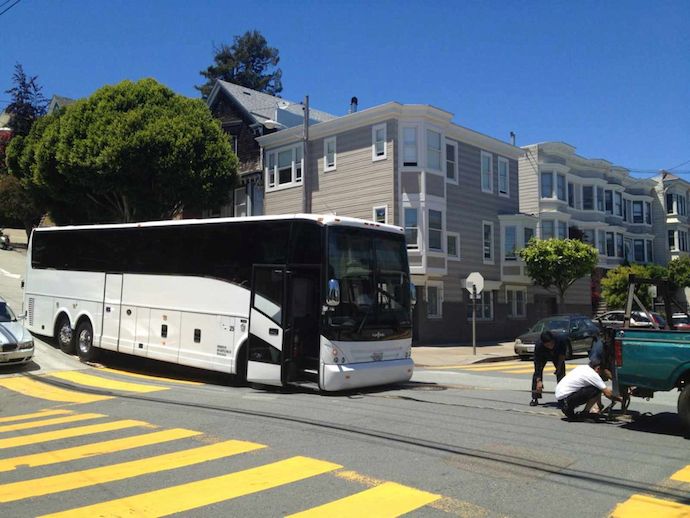
At this point, the hoop armor has yet any wedgelets at the front, although they’d be ineffective anyways against the floor-scraping scoop on Wedgee. Also at this point, I’m still tipsy from the night before and have had three hours of likewise ineffective sleep. Which somehow leads to better driving than ever before. ¯\_(ツ)_/¯
Of course in my next match, I drive myself right out through the pushout.
Two months later I fight Aaron’s Margin of Safety, the new DragonCon champion. It went as you might expect.
So before I get to the design vulnerabilities this revealed, let me get to the crippling mismanaged state that BD4 was in for the ComBugs Cup fight. None of the screws had threadlocker on them because I had taken Big Data apart for shipping. The loose left-side weapon shaft screw comes off with a “PING!” and a black blur at 0:39 in the video, so the shaft is single-supported after that.
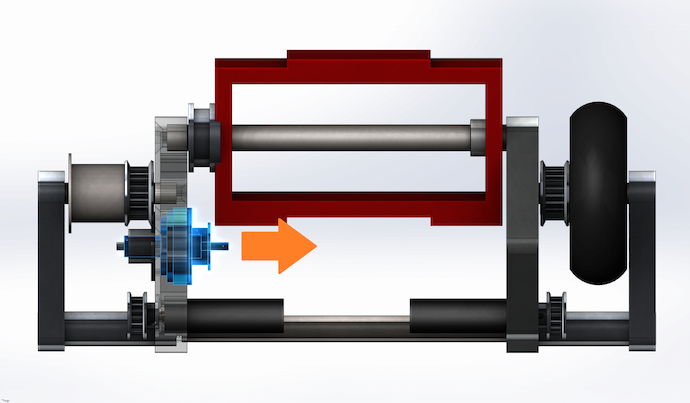
Also, the set screw that holds the weapon motor in its firewall mount had never been tightened. This lets the the motor slide out of position and… into the weapon bar.
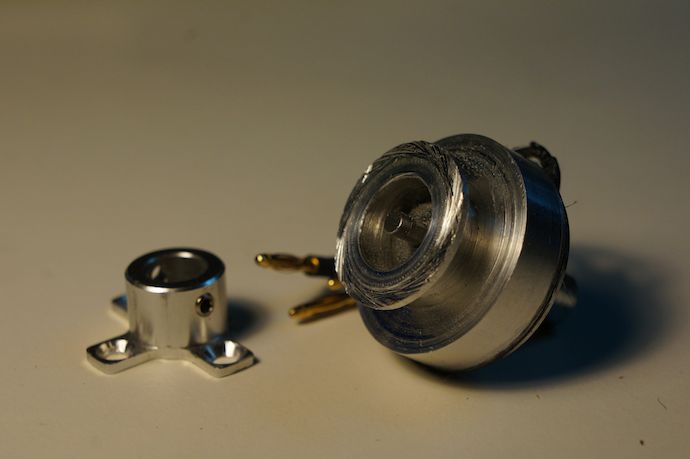
On the other hand, the UHMW hoop armor works well at keeping Margin’s disk away from the vulnerable nylon shell. It’s not low or thick enough to protect the wheels, but that’s a constant danger in any fight against an undercutter.
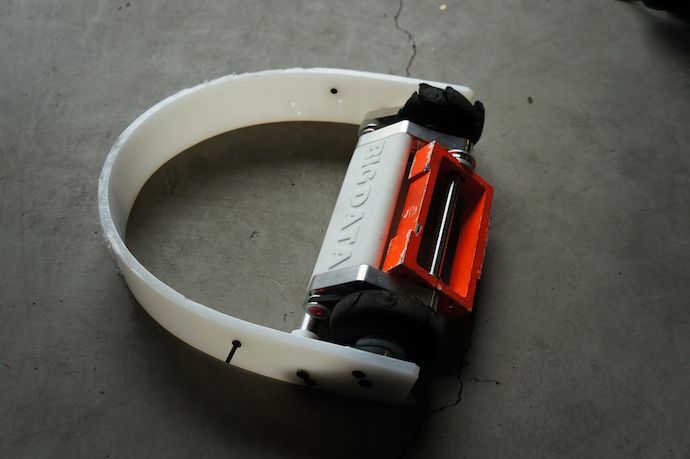
The killing blow (1:36 in the video) was an incredibly vicious hit with Margin’s single tooth engaging the full wall thickness of the chassis piece.
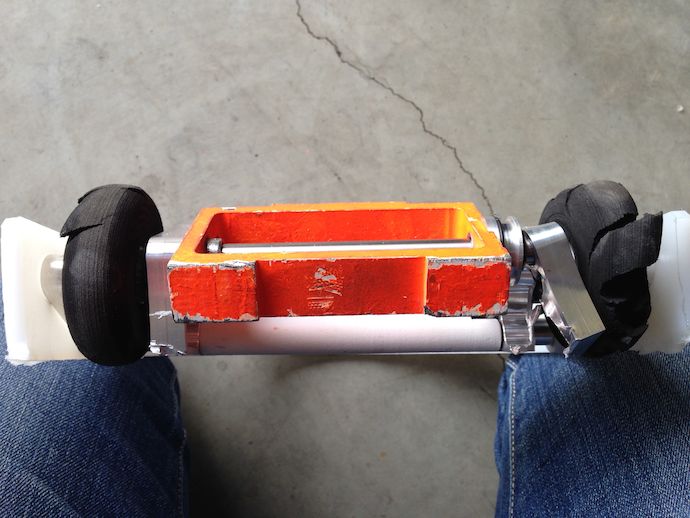
It applied forces towards the outside of the piece (i.e. towards the hogout wall). This concentrates stress into the sharp inside corners of the hogout, causing a fracture that propagated into the walls of the bulkhead.
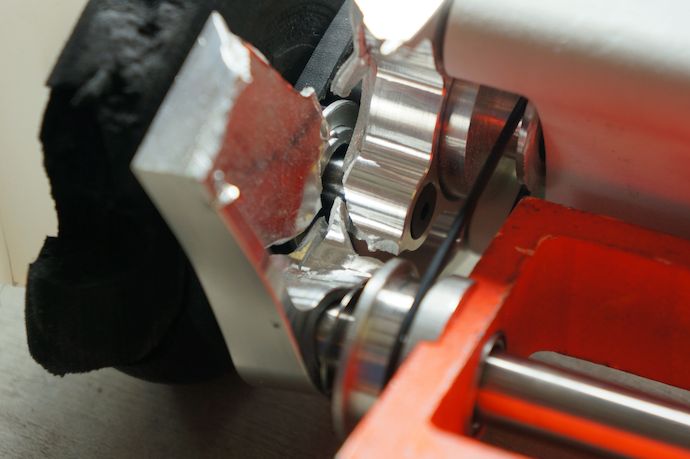
As designed, the piece is meant to break or wear down at the lower corner when hit without distorting the frame geometry. Unfortunately it fractured way more than expected and the loss of the weapon shaft screw allowed the shaft counterbore to distort, making reassembly impossible.
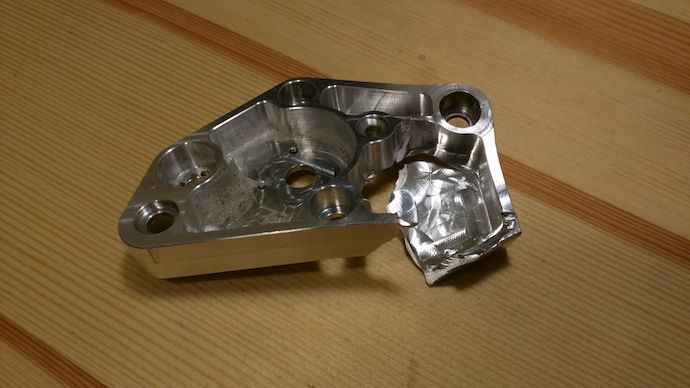
However, the “hard parts” like weapon shaft and wheel axles survived with minimal distortion or thread damage, ready for reuse in another frame. All the motors and drivetrain are fine as well. For my first fight with a spinner, it wasn’t altogether that bad.
It’s an engineer’s natural instinct to tinker with an existing design. However, I’m not going to mess with Big Data too much; I promise to refine and ship a more reliable—not sexier—product.
See you at Motorama 2016?